Help Centre & Support
Mantech UK Limited is dedicated to providing machinery that not only meets but exceeds our customers' expectations. Our comprehensive technical support is tailored to ensure your complete satisfaction.
Telephone
Contact us via telephone at 0121 541 1444 if you’re UK-based or +353 83 833 4614 if you're based in Ireland (including Northern Ireland)
Open a Support Ticket
Access our new support portal to open tickets, chat with our technical team, and track progress—an example of our commitment to meeting customer needs.
Support Guides
As a Mantech customer, you can join our support portal and gain access to our support hub full of guides and helpful tips for your machine.
Customer Focused Service
At Mantech UK Limited, we are dedicated to delivering machinery that not only meets but exceeds our customers' expectations. Our technical support is designed to ensure your experience with us is seamless from start to finish.
From your very first interaction with our sales team to ongoing machinery support, Mantech is committed to being by your side every step of the way. Whether you're seeking guidance, maintenance, or troubleshooting, our professional and knowledgeable team is here to help.
With a vast inventory of spare parts housed in our expansive headquarters in Halesowen, West Midlands, we are fully equipped to support all of our machines. Our skilled support and field engineers go above and beyond, offering everything from routine maintenance to rapid breakdown assistance. At Mantech, your success is our priority, and we’re here to ensure you’re always in expert hands.
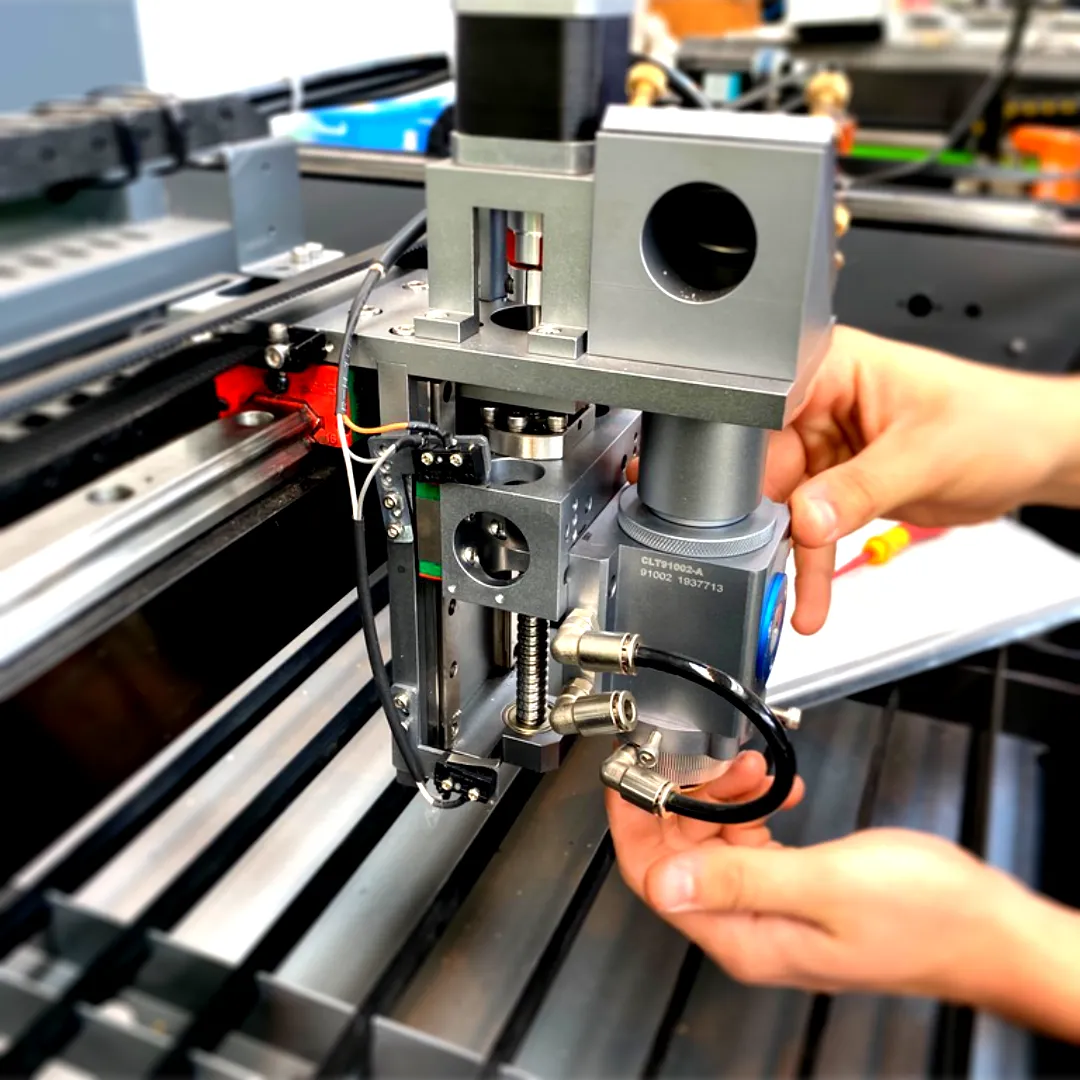
Further Service & Installation Information
Click on each button to find out more.
Delivery & Installation
Delivery & Installation
Our standard service includes delivery to your site and professional installation. For an additional fee, we offer optional offloading.
Our team will guide you on the necessary site preparations and help identify the optimal location for your new equipment. Once on-site, our skilled engineers will handle the installation, commission the machine, verify software functionality, and provide comprehensive operator training to ensure you’re ready to hit the ground running.
Maintenance & Call-outs
Maintenance & Call-outs
Regular, planned maintenance is essential for optimising equipment lifespan and performance. By staying proactive, you can minimise downtime and maintain peak efficiency.
We highly recommend investing in a tailored service plan for your machinery. Our service plans typically cover labour and travel costs, with consumables and replacement parts available at an additional charge. This ensures your equipment remains in top condition while giving you predictable maintenance expenses.
Parts needing replacement under warranty will be done so at no cost.
Parts needing replacement under warranty will be done so at no cost.
Extended Warranties
Extended Warranties
All Mantech-supplied machinery (excluding consumables) comes with standard 1-year parts and labour warranty unless otherwise specified in our quotations. A 24-month warranty is included for certain machines, as clearly noted on the respective product pages.
We are so confident in the quality and durability of our equipment that we offer the option to extend this warranty to 3 years. To qualify, simply enrol in a Service Plan and maintain it throughout the extended warranty period, ensuring your machinery receives regular professional care and support.