Top 5 Reasons Why Your Fabrication Shop Needs a CNC Press Brake 2025 – Boost Efficiency & Precision
In today’s demanding manufacturing landscape, staying competitive means optimizing every aspect of your fabrication process. If you’re still relying on manual or outdated bending methods, you’re likely facing bottlenecks, inconsistencies, and missed opportunities. One piece of machinery stands out as a game-changer for modern metal fabrication: the CNC Press Brake.
But is a CNC Press Brake really necessary for your shop? The answer, for most businesses looking to thrive, is a resounding yes. In this article, we’ll delve into the top 5 critical reasons why investing in a CNC Press Brake isn’t just a good idea – it’s a strategic move to elevate your production, profitability, and product quality.
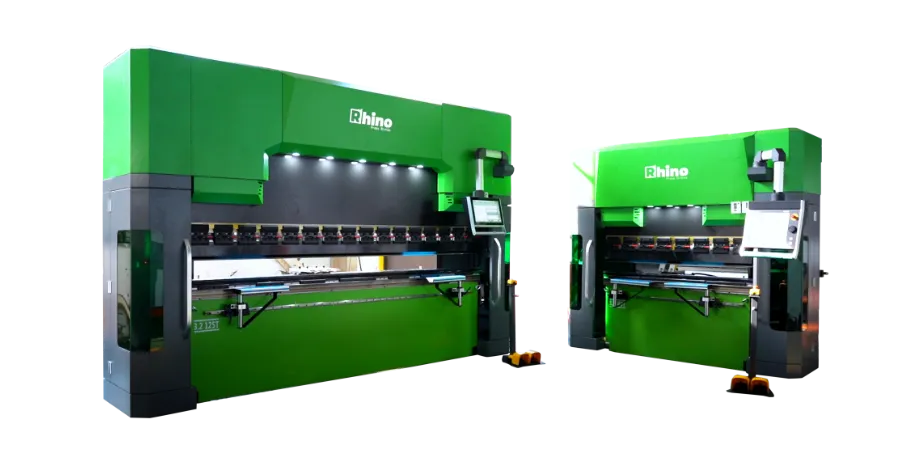
1. Unmatched Precision and Accuracy: Eliminate Costly Errors
One of the most compelling reasons to upgrade to a CNC Press Brake is the unparalleled precision and accuracy it offers compared to manual or conventional press brakes. Manual bending relies heavily on operator skill and can introduce inconsistencies and errors, leading to:
- Scrap Material: Inaccurate bends mean wasted material, directly impacting your bottom line.
- Rework and Delays: Correcting errors is time-consuming, disrupting production schedules and increasing lead times.
- Quality Control Issues: Inconsistent bends can lead to products that don’t meet specifications, damaging your reputation.
CNC Press Brakes solve these problems by utilising computer numerical control to execute bending operations with incredible repeatability and accuracy. Features like:
- Digital Backgauges and Depth Stops: Precisely control the position and depth of each bend.
- Programmable Bend Angles and Sequences: Ensure consistent and complex bends are executed flawlessly every time.
- Real-time Monitoring and Adjustments: Some advanced systems even offer feedback loops to automatically correct for material variations.
The result? Significantly reduced scrap, minimised rework, and products that consistently meet the highest quality standards. For businesses demanding precise metal forming, a CNC Press Brake is not just an advantage – it’s essential.
2. Dramatically Increased Production Speed and Efficiency: Meet Demanding Deadlines
Time is money in manufacturing, and CNC Press Brakes are designed to dramatically accelerate your production speed and efficiency. Compared to manual methods, they offer significant advantages:
- Faster Setup Times: Programs can be loaded quickly, and setup is often automated, drastically reducing changeover times between jobs.
- Automated Bending Sequences: CNC controls execute complex bend sequences automatically, minimising operator intervention and speeding up the entire process.
- Consistent Cycle Times: Every bend is executed with predictable cycle times, allowing for accurate production planning and meeting tight deadlines.
Imagine this: Instead of spending hours manually setting up for each job and painstakingly performing each bend, your operators can load a program and let the CNC Press Brake work its magic. This translates to:
- Higher Throughput: Produce more parts in less time, increasing your overall output.
- Reduced Labor Costs: Automated processes require less operator intervention, freeing up your skilled workforce for other critical tasks.
- Improved Lead Times: Faster production allows you to fulfill orders quicker and gain a competitive edge.
For fabrication shops facing increasing order volumes and tight deadlines, a CNC Press Brake is a powerful tool to unlock unprecedented levels of production speed and efficiency.
3. Enhanced Operator Safety: Protect Your Workforce
Safety should always be a top priority in any fabrication environment. CNC Press Brakes offer significant safety enhancements compared to traditional machines, contributing to a safer and more productive workplace:
- Light Curtains and Safety Interlocks: Modern CNC Press Brakes are equipped with advanced safety systems like light curtains and interlocks that automatically stop the machine if an operator’s hand or body enters the hazardous zone.
- Reduced Manual Handling: Automation reduces the need for operators to be in close proximity to the bending area during operation, minimising the risk of accidents.
- Consistent and Predictable Operation: CNC controlled movements are precise and predictable, reducing the risk of unexpected machine behavior that could lead to injuries.
Investing in a CNC Press Brake demonstrates your commitment to operator safety, leading to:
- Reduced Workplace Accidents: Creating a safer work environment minimizes the risk of injuries and associated costs (medical expenses, lost productivity, insurance premiums).
- Improved Employee Morale: Workers feel safer and more valued when working with modern, safety-focused equipment.
- Compliance with Safety Regulations: Many industries have strict safety regulations, and CNC Press Brakes help you meet or exceed these standards.
By prioritizing safety with a CNC Press Brake, you not only protect your valuable workforce but also create a more efficient and sustainable business operation.
4. Increased Versatility and Complexity: Expand Your Product Offerings
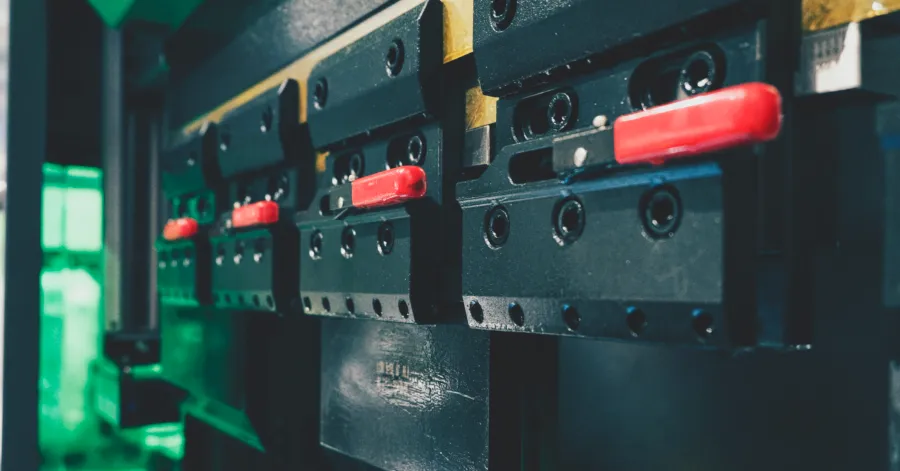
CNC Press Brakes are not just about bending metal; they are about expanding your fabrication capabilities and unlocking new product possibilities. Their versatility allows you to tackle a wider range of projects and offer more complex designs:
- Complex Bend Geometries: CNC controls can handle intricate bend sequences, including multiple bends, hemming, and complex shapes that are difficult or impossible to achieve manually.
- Variety of Materials and Thicknesses: With the right tooling and programming, CNC Press Brakes can work with a wider range of materials (steel, aluminum, stainless steel, etc.) and thicknesses.
- Customisation and Prototyping: Quick program changes and setup make CNC Press Brakes ideal for prototyping and producing customized parts with ease.
This increased versatility translates into:
- Access to New Markets: You can take on projects that require complex bending, opening up opportunities in industries like aerospace, medical, and high-tech manufacturing.
- Product Innovation: Designers and engineers can explore more creative and intricate product designs, knowing your fabrication capabilities can keep up.
- Competitive Differentiation: Offering a wider range of fabrication services sets you apart from competitors who are limited by manual bending methods.
With a CNC Press Brake, you’re not just upgrading your machinery; you’re investing in the future growth and diversification of your business.
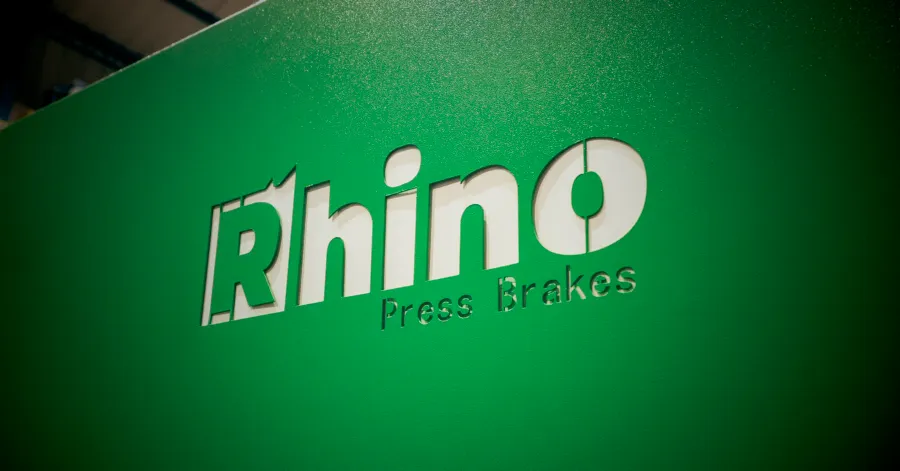
5. Long-Term Cost Savings and ROI: A Smart Investment for the Future
While the initial investment in a CNC Press Brake might seem significant, it’s crucial to consider the long-term cost savings and return on investment (ROI). Over time, a CNC Press Brake pays for itself and generates substantial profits:
- Reduced Labor Costs (as mentioned earlier): Automation requires less operator intervention, lowering labor expenses.
- Minimised Scrap and Rework (as mentioned earlier): Precision bending reduces material waste and rework, saving on material and labor costs.
- Increased Production Capacity (as mentioned earlier): Higher throughput leads to increased revenue and faster order fulfillment.
- Lower Maintenance Costs (compared to older machines): Modern CNC Press Brakes are often designed for reliability and require less frequent and less costly maintenance.
When you factor in these savings, along with the increased efficiency, productivity, and expanded capabilities, the ROI on a CNC Press Brake becomes clear. It’s not just an expense; it’s a strategic investment that delivers tangible financial benefits, including:
- Faster Payback Period: The combined savings and increased revenue accelerate the payback period for your investment.
- Improved Profit Margins: Reduced costs and increased efficiency directly contribute to higher profit margins.
- Enhanced Business Value: A modern, efficient, and profitable fabrication shop is a more valuable asset.
Investing in a CNC Press Brake is a smart financial decision that positions your business for long-term success and profitability in the competitive metal fabrication market.
The transition to a CNC Press Brake is more than just an equipment upgrade; it’s a transformation of your entire fabrication operation. From unmatched precision and speed to enhanced safety and expanded capabilities, the top 5 reasons we’ve outlined clearly demonstrate the critical need for a CNC Press Brake in any modern fabrication shop.
Stop letting outdated bending methods hold your business back. Embrace the power of CNC technology and unlock a new era of efficiency, precision, and profitability.
Ready to take the next step?
Press Brakes