CNC Router Machines – The Importance Of Regular Maintenance
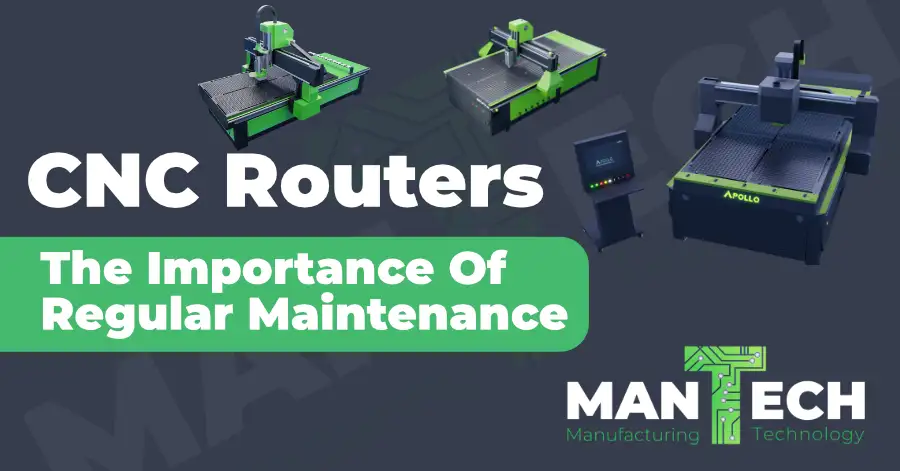
CNC Router Machines – The Importance Of Regular Maintenance
It’s imperative that we take an interest in the general upkeep of our industrial machinery equipment, ensuring longevity and the whole user experience. We’ve attached a brief outline of the regular maintenance you should be undertaking with your CNC Machine below.
The Benefits of Regular Maintenance
Increased Machine Life:
Regular CNC router machine maintenance can significantly extend its life, and save on replacement costs. This is because maintenance tasks, such as cleaning and lubricating the machine, prevent wear and tear, and reduce the risk of breakdowns and failures over time.
Improved Machine Performance:
Regular maintenance can also help to improve the performance of your CNC router machine. Maintenance tasks can help to resolve minor issues before they become problematic and require an engineer’s visit. For example, if a belt or spindle is wearing out, it can be replaced before it snaps and cause damage to other components within the machine.
Enhanced Accuracy:
Regular maintenance can also help to maintain the accuracy of your CNC router machine. For example, if the machine’s bearings or guides are worn or dirty, it can cause the machine to vibrate, which will adversely affect its accuracy. Regular maintenance tasks, such as cleaning and lubricating the guides and bearings, can help to maintain their accuracy and extend their life, therefore creating a more accurate production output.
Reduced Downtime:
Regular maintenance can help to reduce the amount of downtime experienced by your CNC router machine. This is because, as mentioned above, maintenance tasks can resolve minor issues before they become major problems and cause the machine to break down. This, in turn, will increase your machine’s availability and efficiency.
What to Include in Your Maintenance Plan
Regular maintenance can help to reduce the amount of downtime experienced by your CNC router machine. This is because, as mentioned above, maintenance tasks can resolve minor issues before they become major problems and cause the machine to break down. This, in turn, will increase your machine’s availability and efficiency.
Cleaning:
Cleaning your CNC router regularly is crucial to its performance and longevity. This includes cleaning the machine’s surfaces, guides, and bearings, as well as removing any dust or debris that has accumulated inside the machine.
Lubrication:
Lubricating the machine’s moving parts, such as its spindle, bearings, and guides, is important to prevent wear and tear and maintain accuracy. You should lubricate the machine regularly, as recommended by the manufacturer, and replace the lubricant when it becomes dirty or contaminated.
Inspection:
You should inspect your CNC router regularly to identify any issues or wear and tear that need to be addressed. This includes checking the machine’s belts, bearings, spindle, and guides for any signs of wear or damage, once any damage has been identified, it is recommended that you get in touch with your CNC router manufacturer or supplier.
Calibration:
You should carefully calibrate your CNC router regularly to ensure that it continues to operate at its best performance. This includes checking the machine’s accuracy and adjusting its settings as necessary, following your manufacturer’s guidelines.
Replacement of Worn Parts:
You should replace any worn parts on your CNC router as soon as they start to show signs of wear or damage to prevent any further deterioration. This could include belts, bearings, spindles, and guides.
In Conclusion
Regular maintenance is crucial to the longevity and performance of your CNC router machine. By including cleaning, lubrication, inspection, calibration, and replacement of worn parts in your maintenance plan, you can ensure that your machine continues to operate at its best and provide you with the high precision, repeatability, and efficiency that you need for years to come.
CNC Machines
CNC Routers