Choosing The Best CNC Router
Choosing the Best CNC Router for your business or application.
Introduction
Understanding CNC Routers
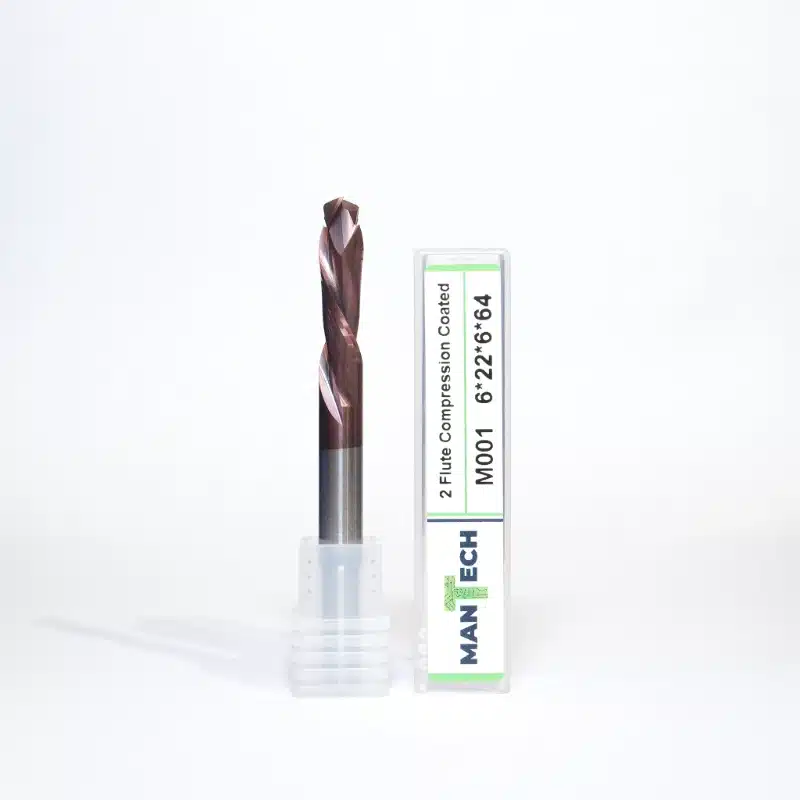
Types of CNC Routers
Factors to Consider When Choosing a CNC Router
Purpose and Project Scope: Determine the primary use of the CNC router, whether for intricate artistic work, industrial manufacturing, or hobbyist projects. This decision will influence the type of machine and features required.
Workspace Constraints: Assess the available space in your workshop or factory. The size of the CNC router should fit comfortably in your workspace without hindering operations.
Budget Considerations: CNC routers vary significantly in price. Define your budget early on and consider the balance between cost and the features you need.
Software and Compatibility: The software that operates the CNC router is crucial. Ensure that it is compatible with your design software and easy to use.
Precision and Accuracy Needs: Consider the level of precision required for your projects. Higher precision machines tend to be more expensive, so align this with your project needs.
Each of these factors plays a vital role in selecting the right CNC router, aligning with your specific requirements and constraints.
Advanced Features and Technologies in CNC Routers
Automated Tool Changing (ATC): This feature allows the machine to automatically switch between different tools during a job, significantly reducing manual intervention and downtime. ATC systems are a boon for complex projects requiring multiple tool types, enhancing productivity and operational efficiency.
High-Performance Spindles: Contemporary CNC routers often come with powerful, air-cooled spindles. These spindles can operate at high speeds, crucial for precision cutting and working with a diverse range of materials.
Advanced Motion Control Systems: The latest CNC routers are integrated with sophisticated motion control systems. These systems offer intuitive interfaces, often with touchscreen control, and are designed for ease of use. Features like network capability and advanced algorithms for efficient operation are common.
Software Integration and Simulation: Modern CNC routers are compatible with advanced software for project simulation, g-code editing, and efficient operation. This allows operators to anticipate project timelines, reduce material waste, and make adjustments easily.
Enhanced Spindle and Tool Change Control: Precision control over spindle speeds and tool changes is a key feature in newer models. This allows for finer adjustments and better control over the cutting process, leading to higher-quality results and extended tool life.
Material Versatility: Today’s CNC routers are capable of handling a wide variety of materials, from woods and plastics to soft metals and composites. This versatility makes them suitable for a range of industries and applications.
These advancements represent a significant evolution in CNC router technology, making them more efficient, versatile, and user-friendly. They cater to the needs of various industries, from bespoke furniture making to aerospace engineering, offering high-quality results and increased productivity.
For more detailed information on the specific features and capabilities of contemporary CNC routers, consulting with manufacturers or industry experts is advisable.
CNC Router Maintenance
Routine Maintenance: Daily tasks like cleaning guide rails, greasing, and inspecting cutters are essential for smooth operation.
Scheduled Maintenance: Weekly, monthly, quarterly, and bi-annual maintenance routines are outlined, emphasising tasks like cleaning CNC components, checking vacuum pumps, and ensuring the integrity of bearings and belts.
Specialised Maintenance Procedures: Instructions on specific maintenance tasks like vacuum bed and sacrificial surface best
Practices. These include best practices for vacuum bed use and sacrificial surface management, which are crucial for optimal grip and precision during machining processes.
Comprehensive Guides for Advanced Maintenance:
Mantech provides detailed guides for more complex maintenance procedures. These include instructions for checking and adjusting various machine components and ensuring the machine’s electrical and mechanical systems are in top condition.
Support and Resources: Mantech offers a robust support system with a range of self-help guides and videos. These resources are designed to assist users in effectively maintaining and troubleshooting their CNC routers.
For detailed maintenance instructions and best practices, you are more than welcome to contact our team of service engineers by calling them on 0121 541 1444.
Conclusion
The advancements in CNC technology have made these machines more efficient, precise, and versatile than ever before. Whether you’re a small business, a large industrial operation, or a creative individual, there’s a CNC router that fits your requirements.
We encourage you to further explore the potential of CNC routers for your projects. Consider reaching out to ourselves or other suppliers for detailed consultations, demos, and more information to make an informed decision that aligns with your goals and budget.